Kérj ajánlatot még ma, hogy segíteni tudjunk!
Minőségi weboldalak, prémium kivitelézése rövid határidővel. kapcsolat
TEMI Slider Plugin WordPress oldalakhoz
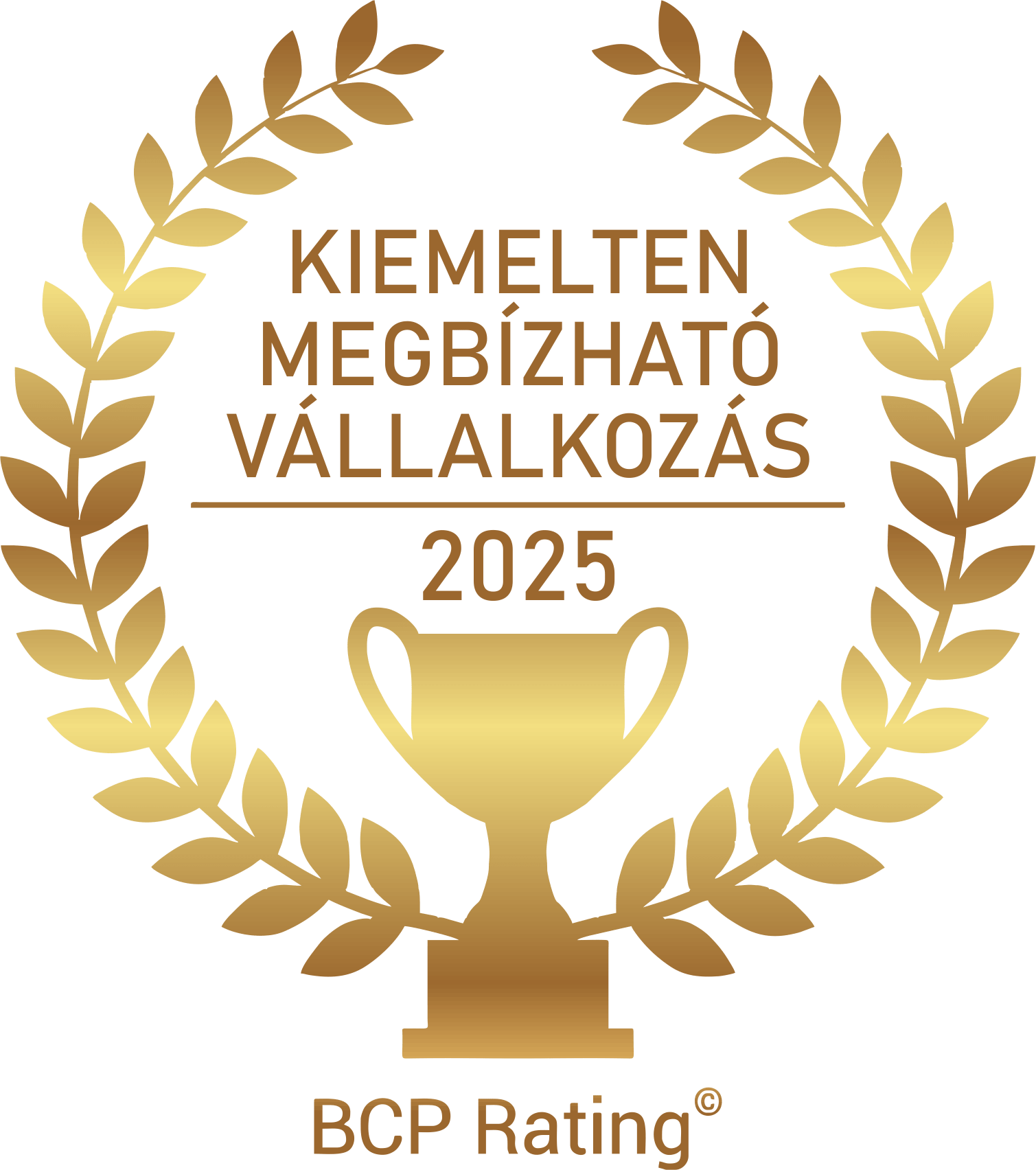
Domain és tárhely választása
A tökéletes domain név kiválasztása kulcsfontosságú a sikeres online jelenlét szempontjából. Csapatunk segítségével megtalálhatja azt a domain nevet, amely leginkább tükrözi vállalkozása szellemiségét és hosszú távon is támogatja brandépítési céljait. Nem csak a név kiválasztásában nyújtunk segítséget, hanem abban is, hogy a megfelelő tárhely-szolgáltatást válassza, amely megfelel weboldala technikai követelményeinek és látogatottsági szintjének. Intézkedünk a domain regisztrációjáról és a tárhely beállításáról, így Ön nyugodtan összpontosíthat üzleti tevékenységére, míg mi gondoskodunk az online infrastruktúráról.
Weboldal tervezése
Weboldalad megtervezéséhez közösen áttekintjük a fontos paramétereket. Vizualizálni fogom neked a weboldal vázszerkezetét, amivel el tudunk indulni a fejlesztés felé. Ez az első lépés abban, hogy a látványterved valósággá váljon, miközben biztosítjuk, hogy minden részlet tökéletesen illeszkedjen vállalkozásod személyiségéhez és célkitűzéseihez.
SEO barát oldalak
Komoly kutatásokat és munkálatokat végzek annak érdekében, hogy weboldaladat minnél többen megtalálják a megfelelő kulcsszó alapján. Komplex SEO szolgáltatásokkal javítjuk weboldala Google-beli rangsorolását, növelve ezzel online láthatóságát. Tervezünk és menedzselünk PPC kampányokat is, hogy üzleti céljaihoz mérten növeljük weboldalának forgalmát. Az sem árt, ha google is lát! 😉
Aktuális Cikkek
Te melyiket szereted? weboldal
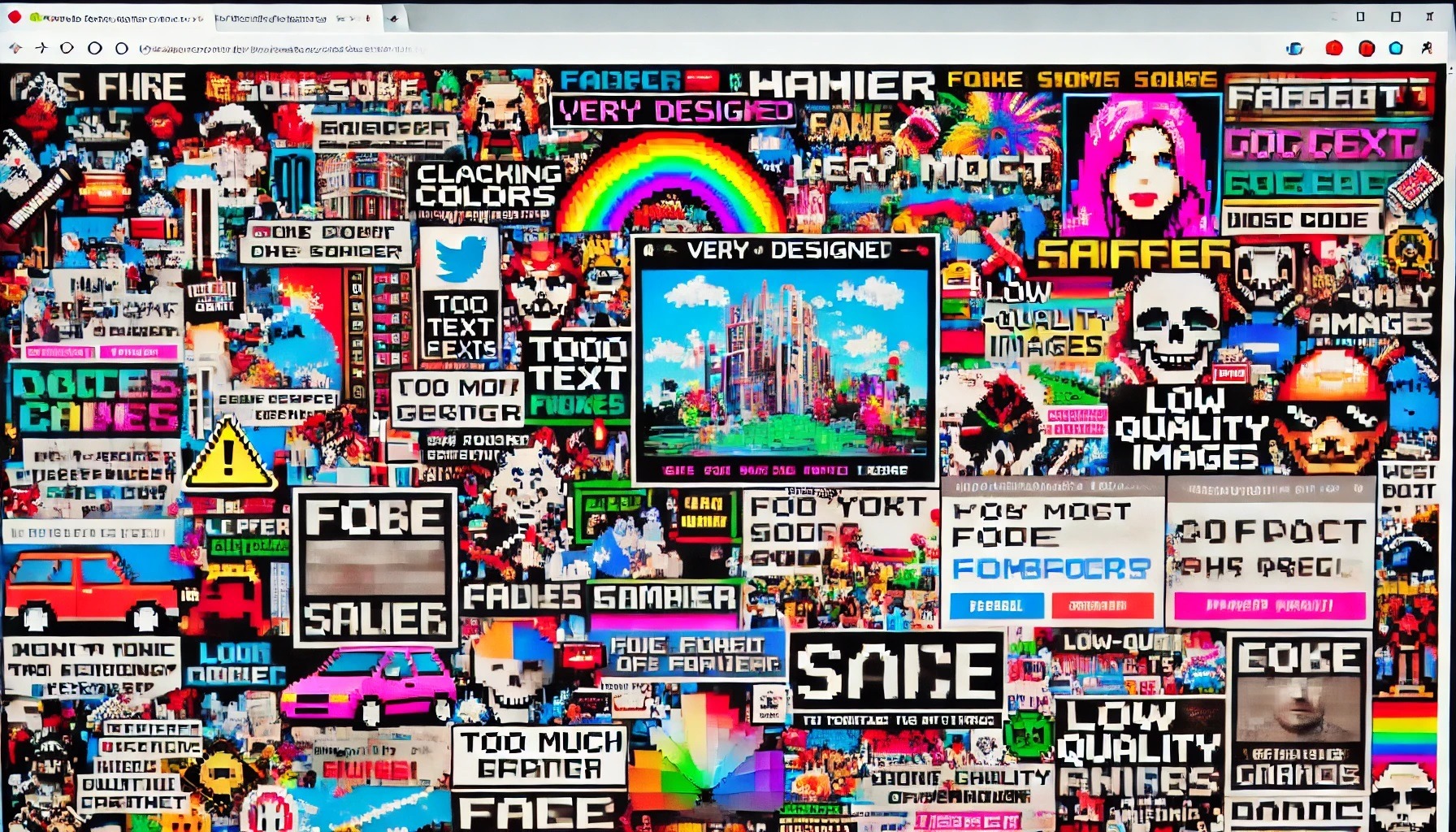
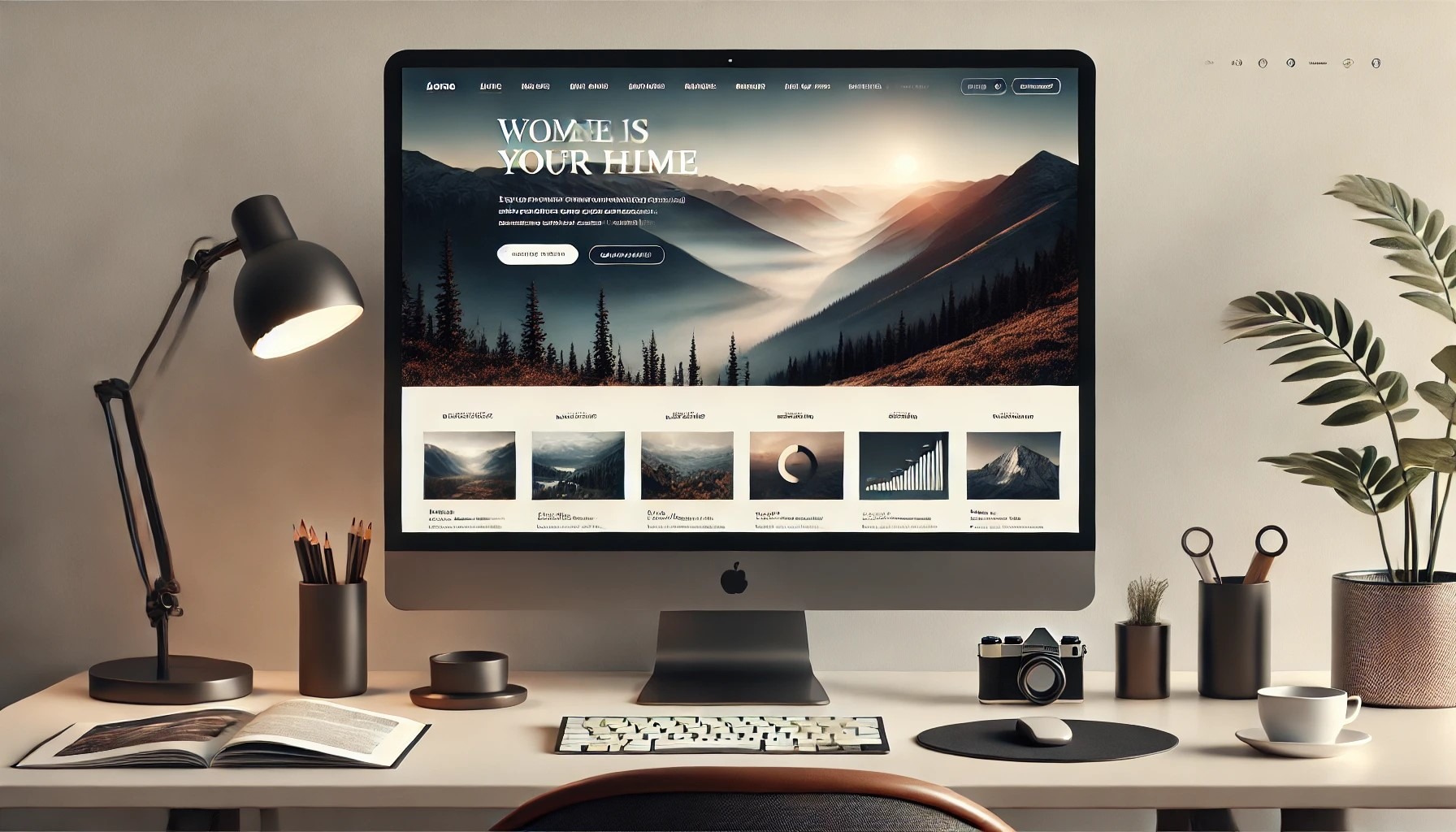